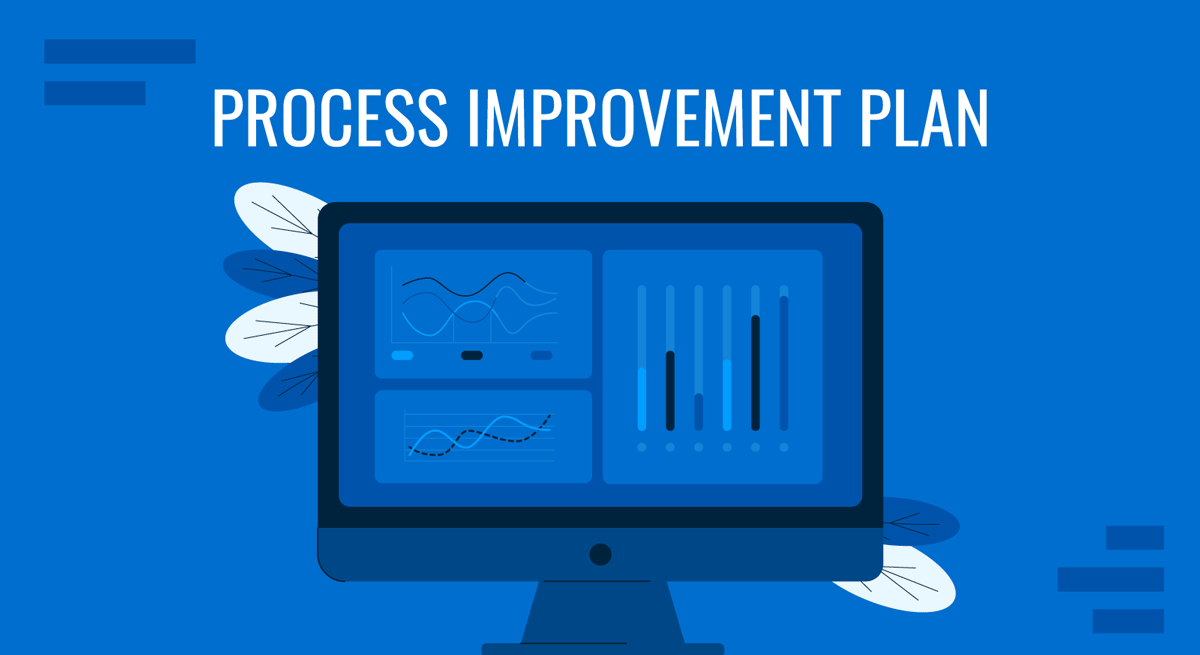
When you run a business, staying ahead of the curve is not just a goal but a necessity. Technologies improve. Market conditions shift. Customer preferences change. Businesses that fail to keep up with these changes risk falling behind their competitors or, even worse, closing down.
That’s why every organization, no matter how well their business is running, must proactively seek opportunities for process improvement to adapt to changing times.
Table of Contents
- What Is a Process Improvement Plan?
- Common Methodologies of Process Improvement
- How to Make a Process Improvement Plan
- Conclusion
What Is a Process Improvement Plan?
Ingrained processes may become comfortable and familiar, but they can hinder growth and efficiency without regular assessment and optimization. A Process Improvement Plan (PIP) helps in this regard by providing a structured approach to analyzing, optimizing, and refining existing organizational processes.
Whether it’s a manufacturing procedure or a customer service workflow, a PIP provides a systematic framework to identify areas that need enhancement and implement changes to maximize efficiency and effectiveness.
Process improvement is part of the monitoring phase of the project management lifecycle. Project managers and teams monitor project progress, performance, and key metrics. Process improvement initiatives may be initiated to enhance project outcomes if any inefficiencies or bottlenecks are identified during monitoring.
Benefits of Working with a Process Improvement Plan
A well-executed PIP offers numerous advantages, including:
- Enhanced Efficiency: Identifying and rectifying inefficiencies leads to optimized workflows and reduced operational waste.
- Improved Quality: Streamlined processes result in higher-quality outputs and fewer errors.
- Increased Productivity: With streamlined workflows, teams can focus on value-adding tasks, leading to increased productivity.
- Cost Savings: Process improvements spot broken procedures that can have significant financial implications, ultimately positively impacting the organization’s bottom line.
Common Methodologies of Process Improvement
Process improvement relies on methodologies to provide guided approaches and tools for identifying inefficiencies and achieving desired outcomes. While project management methodologies focus on successfully delivering specific projects, process improvement methodologies are designed to enhance ongoing operations within an organization. These two methodologies serve distinct purposes but can complement each other to drive overall business success.
Here are the most commonly used process improvement methodologies:
1. Six Sigma DMAIC Process
DMAIC is a widely embraced and structured process improvement methodology that is a key component of the Six Sigma approach. It is an evolution of the PDSA (Plan-Do-Study-Act) cycle that presents a systematic roadmap adaptable to any organization seeking “incremental improvements” on existing processes to attain superior quality and predictable outcomes.
DMAIC has five phases and stands for:
- Define the problem or opportunity for improvement.
- Measure the current performance of a given process.
- Analyze the underlying causes of problems and inefficiencies.
- Improve processes to address the root causes of the problem.
- Control improved processes by implementing the measurement plan.
The keyword in DMAIC is “incremental improvement.” While DMAIC is an effective methodology for continuous improvement and optimizing existing processes, it may not be the best fit for projects that require radical or exponential improvements or when designing entirely new processes.
Let’s see an example of this tool by using this case study: SoftTec, a software development company, is looking to improve the situation of one of its projects. One web application they created frequently experiences performance issues and crashes during peak user times, which in turn delivers a poor user experience.
Define:
- Reduce application crashes by 70% during peak hours.
- Improve the average response time by at least 40% during those peak hours.
- Enhance the overall user satisfaction based on surveys.
Measure
- List down the number of app crashes during the defined time slot per week.
- Measure the avg. response time during those peak hours per week.
- Evaluate the user feedback surveys in terms of user satisfaction with the app on a scale of 1-10.
Analyze
- Insufficient server resources to handle the user demand during peak hours.
- Inefficient database queries (human error or lack of knowledge).
- Code bottlenecks or suboptimal algorithms.
Improve
- Upgrade the server infrastructure to handle increased traffic during peak hours.
- Optimize the database queries to speed up data retrieval.
- Implement code reviews and performance actions into critical parts of the process.
Control
- Implement real-time monitoring of the performance metrics.
- Foster a culture of continuous education for the Development team.
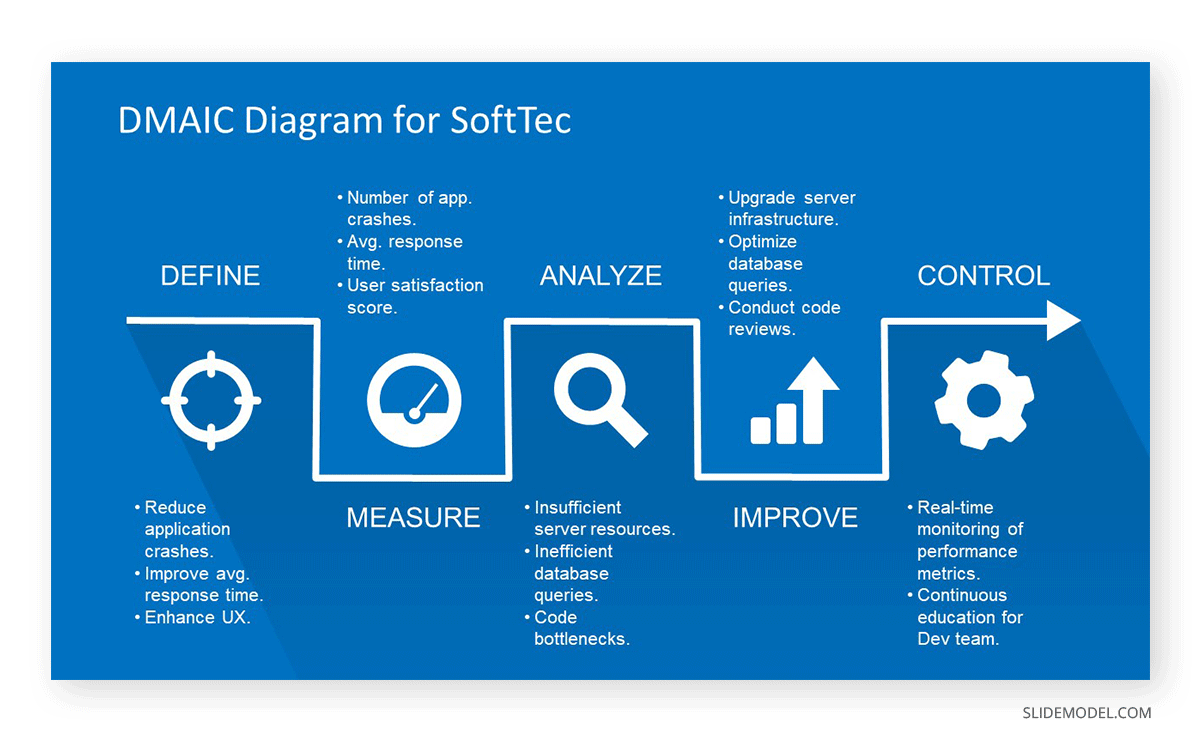
Organizations often turn to the modified DMADV (Define—Measure—Analyze—Design—Verify) methodology for scenarios that demand significant breakthroughs, also known as DFSS (Design for Six Sigma).
2. Improvement Kata
Mike Rother introduced The Improvement Kata concept in his book “Toyota Kata.” Drawing inspiration from the continuous improvement practices of the Japanese car manufacturer Toyota, Rother adapted and extended these principles to help organizations embrace a culture of lean production.
The Improvement Kata emphasizes the development of habits and “muscle memory” that foster a mindset of continuous improvement throughout the organization. It is not just about the “systematic pursuit of desired conditions”; instead, it seeks to instill a way of thinking that empowers employees to think more openly, experiment, and constantly seek better solutions.
This improvement methodology has four steps:
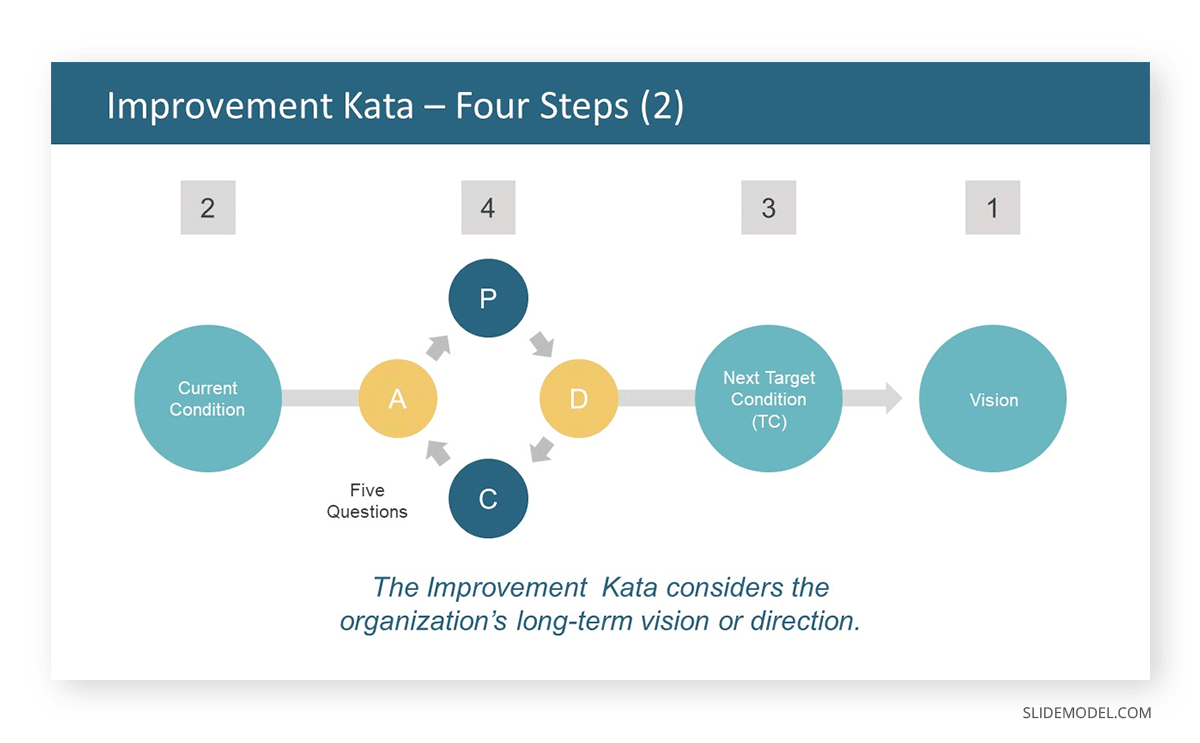
- Understand the distant direction (vision) to be achieved
- Grasp the current condition
- Establish the NEXT target condition (time-specific goal beyond your current knowledge limit)
- Experiment against obstacles to achieve the target condition
3. Total Quality Management (TQM)
Total Quality Management (TQM) is a management method born from a belief that pursuing quality should be an ongoing and cooperative effort involving everyone in an organization, from top management to the lowest-level employees and customers. It’s an evolution of various quality management approaches from Walter A. Shewhart and W. Edwards Deming, bringing together the best practices from each methodology.
The fundamental principles of Total Quality Management include:
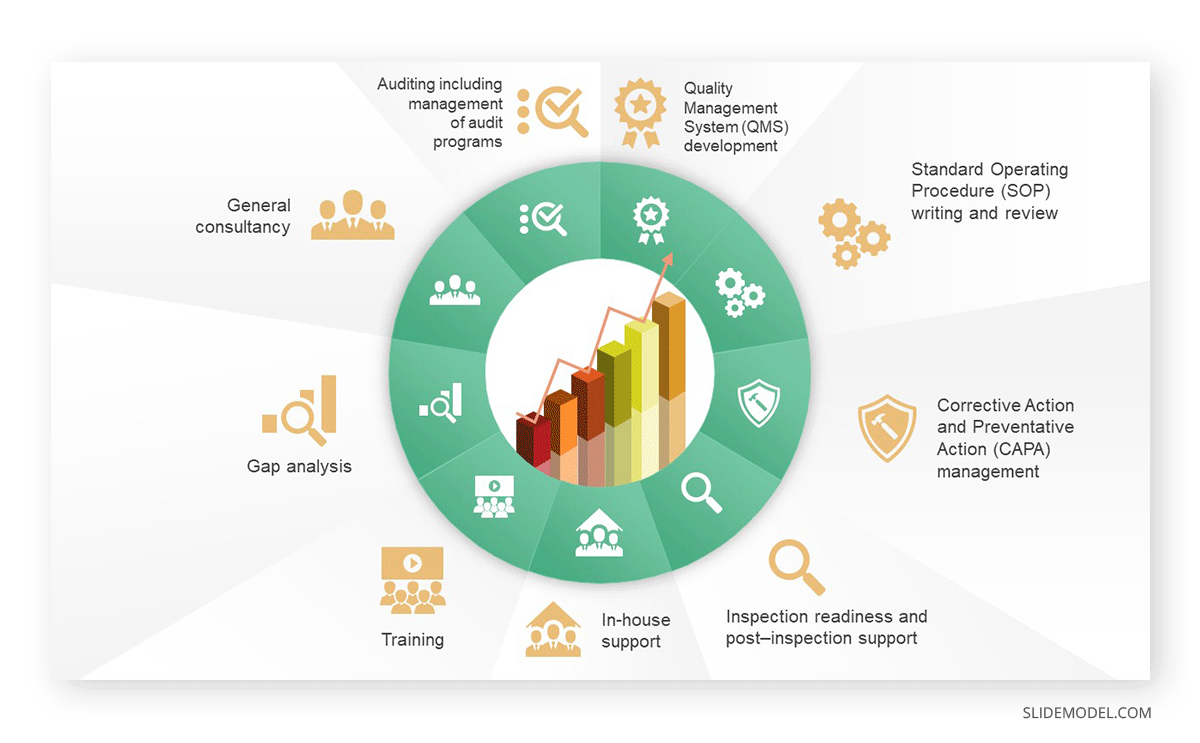
- Customer Focus: Understand and meet customer requirements and put them at the center of all activities.
- Employee Involvement: Encourage active participation from employees in problem-solving, decision-making, and process improvement initiatives.
- Process-centered: Create well-defined and well-managed processes to ensure consistency and quality in the final output.
- Integrated Systems: Processes and functions within an organization should be interconnected and aligned toward the common goal, avoiding silos and focusing on collaboration.
- Systematic approach: Use a methodical approach to managing quality to achieve goals.
- Data-Driven Decision-Making: Eliminate guesswork and use data to ensure that quantifiable facts back decisions.
- Communication: Implement transparent communication channels within the organization to help disseminate information about quality goals, progress, and changes effectively.
- Continues Improvement: Promote the idea of the ongoing pursuit of process improvement to meet or exceed customer expectations.
How to Make a Process Improvement Plan
While distinct in their approaches, process improvement methodologies share some common activities and principles. These activities reflect the core elements necessary to drive successful process improvement initiatives.
In this section, let’s zero in on the shared steps you can take to build an effective process improvement plan.
1. Select a Specific Process to Improve
It’s important to take a healthy dose of changes within an organization. As the famous proverb says, don’t bite off more than you can chew. Trying to implement abrupt and multiple changes within your activities may cause multiple problems, like spreading resources thinly and overwhelming your employees.
Focus on one process that has strategic significance within your organization. By selecting a specific process to improve, you can concentrate your efforts, resources, and attention, increasing the likelihood of success.
Think about the following when considering processes that need improvement:
- Which process is the most critical to the business?
- Which process offers quick wins or immediate benefits?
- Which process is causing the most significant challenges or bottlenecks?
You may use a simple prioritization matrix to determine which process improvement to focus on first.
Let’s assume you are a manager of a grocery delivery service, and you want to improve your overall customer satisfaction rate. You have identified four processes that require improvement:
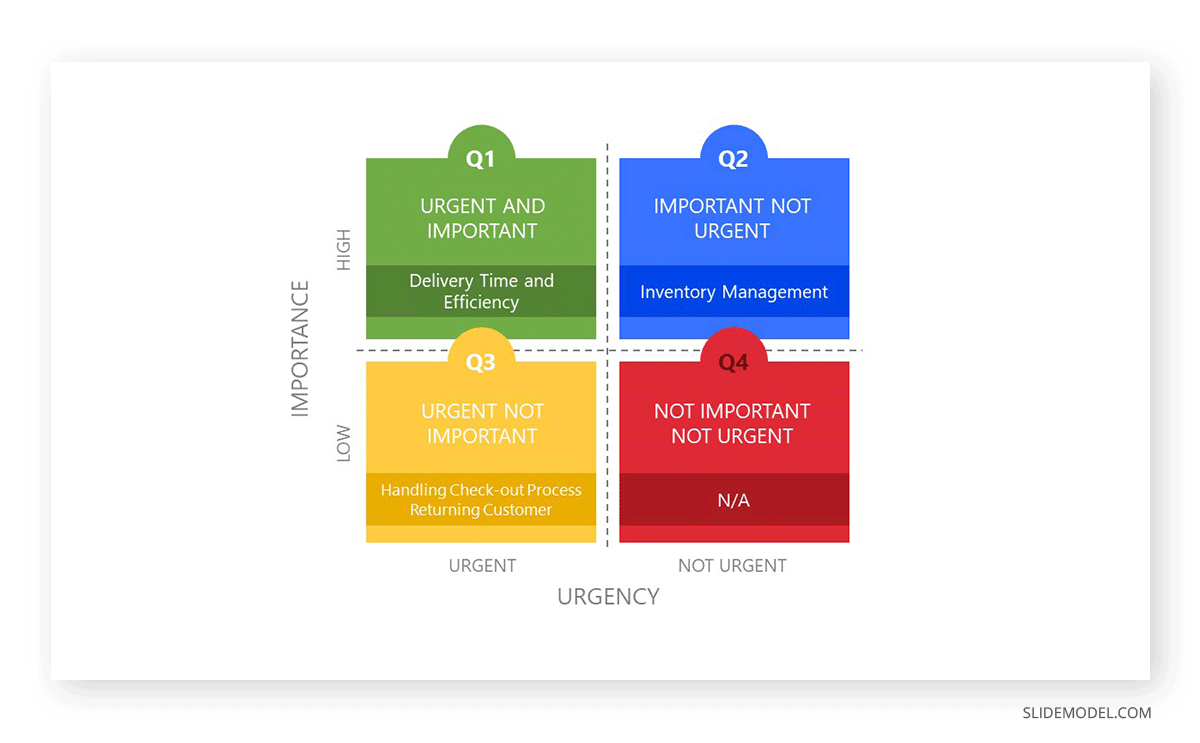
Based on the prioritization matrix, it’s clear that the “Delivery Time and Efficiency” process should be the first area of improvement to focus on. Improving delivery speed and efficiency can immediately impact customer satisfaction, leading to higher retention rates and positive word-of-mouth referrals.
2. Set Goals
A project without a clear goal is often the worst kind of project. When there is no well-defined scope and set objectives, such projects encounter numerous challenges and setbacks, making measuring progress and success difficult.
It would help to follow the SMART (Specific, Measurable, Achievable, Relevant, Time-bound) formula when setting the end goal of your process improvement endeavor. This will help establish metrics and key performance indicators (KPIs) to quantify the results of the improvement efforts.
In our grocery delivery service example, the goal could be a 90% reduction in failed delivery attempts within the next two months.
3. Map the Current Process
The next step is to understand how the current workflow operates. Collaborating with the team members is paramount to gathering insights and details about each step, including the common pain points encountered.
Create a flowchart or process map that illustrates the sequence of activities, decision points, and interactions involved in the process. Then, analyze the process map to identify bottlenecks or areas where delays occur.
Here’s a possible flowchart for the grocery delivery service example.
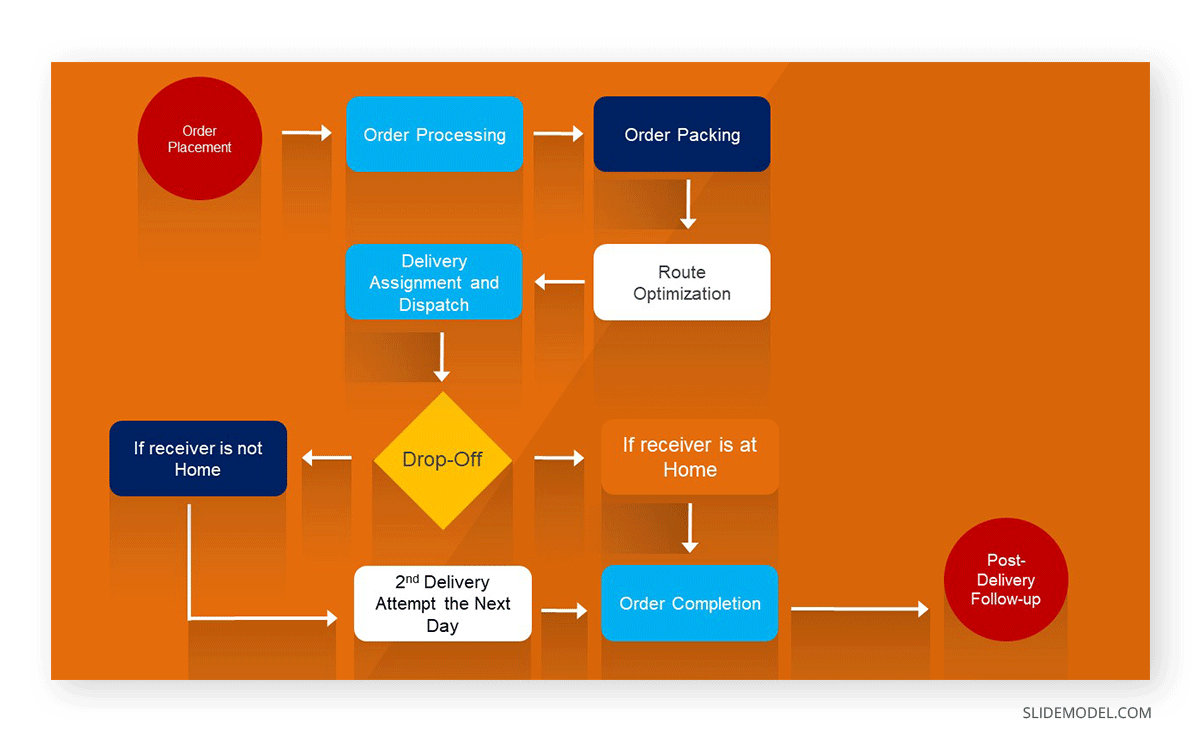
As you can see, a delay in delivery may arise when the receiver of the parcel is not at home. A second delivery attempt constitutes additional expenses for the company, like fuel expenses.
4. Redesign the Process and Allocate Resources
After mapping the process and identifying areas that require improvement, the next step in the process improvement journey is to redesign the process. It involves making intentional changes to the existing workflow to eliminate inefficiencies.
You may consider several solutions. However, weighing your options concerning the resources you are willing to allocate is important. Consider the potential return on investment (ROI) for each solution.
In our example, the grocery delivery service may ask customers upon checkout to select a delivery date based on a fixed time window that suits their convenience. This may require several technologies, like a time slot management system. Still, it offers cost-saving benefits such as reduced delivery fleet downtime, optimally filling delivery vehicles, and reducing failed delivery attempts.
5. Test the Redesigned Process
Testing is a crucial step before implementing any process improvement plan. This step will ensure that the proposed changes deliver the desired outcomes without causing unintended negative consequences.
Test the process improvements on a small scale involving the end-users, and collect feedback. Use the data you gather to make additional changes to the plan.
Going back to the grocery delivery service, they may select a specific geographic area or a small group of customers to participate in the pilot test of the time slot management system. This allows for a controlled and focused testing environment.
6. Present and Implement
It’s time to introduce the process improvement plan and implement the changes to the stakeholders. At this stage, the organization should ensure alignment of expectations with the team members so everyone understands their roles and responsibilities. Provide training when necessary. Additionally, securing buy-in and approval from key decision-makers is essential for a successful implementation.
Using the ADKAR Model presentation can address the key elements of introducing and implementing the process improvement plan. It focuses on individual change management and helps stakeholders understand and embrace the proposed changes.
7. Monitor and Iterate
Finally, keep looking for opportunities to optimize your workflow. As mentioned, improving your processes is an ongoing activity. So, keep assessing the performance of the redesigned process, gathering feedback, and making further improvements to enhance its effectiveness and efficiency.
Conclusion
Process improvement is not just an option but a necessity for organizations to stay competitive and relevant. This vital practice elevates efficiency, eliminates ineffective procedures, and reduces costs. Use the methodologies and tools we discussed in this article to systematically analyze your processes and navigate them toward the path of success.